Recycling "breakthrough" could usher in zero-emissions cement
Researchers at the University of Cambridge have devised a way of cheaply producing low-carbon concrete at scale by making use of waste cement and the steel industry's electric arc furnaces.
The method developed by the engineers involves recycling old cement from demolished buildings by heating it up and reactivating the compounds within it.
Key to the innovation is how this process is executed: by piggybacking off the existing electric-powered furnaces used to recycle steel.
Recycling innovation a "breakthrough for the construction industry"
Cement is the key ingredient in concrete and responsible for around 90 per cent of the material's substantial carbon emissions.
The Cambridge researchers' approach addresses both of the major sources of those emissions: the chemical reaction as limestone is turned into new cement, and the firing of fuels to power the high-heat kilns needed for that process.
Cambridge academic Julian Allwood said that the innovation represented "a breakthrough for the construction industry" and that the research team believed it would become "the world's first process for making zero-emissions cement".
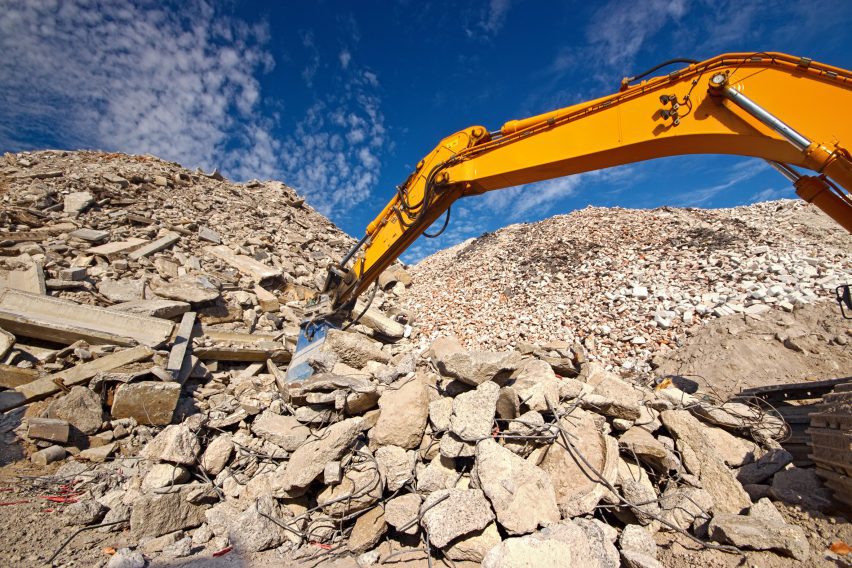
"We know that if in future that furnace is powered by electricity that has no emissions, our process could make cement with no emissions whatsoever," said Allwood.
The team have started a private company to commercialise their product, which they are calling Cambridge Electric Cement, and say they could provide about a third of the UK's cement needs within ten years.
They have successfully tested their method at a steel recycling facility. But a full industrial-scale test later this month – where 60 tonnes of cement should be produced in two hours – will give a more conclusive indication about its scalability.
Recycled cement becomes part of steel slag in simple process
The process involved is relatively simple. After a building's demolition, its concrete is crushed to the point where the cement can be separated from the aggregates.
This used cement is taken to a steel furnace and used in place of lime as the "flux" – the cleaning agent used in the recycling process to remove impurities from the molten metal. This is possible because cement and lime have a similar calcium oxide-based composition.
The flux combines with the impurities to form slag – a byproduct that rises to the top of the molten steel and can be easily separated off. At this point, if the cement-based slag is removed and cooled quickly, it turns into high-quality Portland cement.
According to the researchers, this recycled cement is expected to be as durable as any other cement in the UK, because it has the same chemical composition.
It also has an advantage over other low-carbon concrete solutions in development, they say, because it uses existing processes, equipment and standards, with no substantial additional costs for either the concrete or steel industries.
This means that whether the cement is made in co-production with steel recycling or on its own using the same equipment, it should be able to be scaled rapidly.
"Miracle" cement alone is not the answer
Up until now, most solutions have involved replacing part of the cement content of concrete with alternative materials such as fly ash. But its cement component could never be replaced completely because it is necessary for chemical activation, meaning some emissions always remained.
However, the researchers stress that their electric cement alone cannot solve the problems of concrete-related carbon emissions.
"Producing zero emissions cement is an absolute miracle, but we've also got to reduce the amount of cement and concrete we use," said Allwood. "Concrete is cheap, strong and can be made almost anywhere, but we just use far too much of it."
"We could dramatically reduce the amount of concrete we use without any reduction in safety, but there needs to be political will to make that happen," he added.
The Cambridge team's process and findings are documented in a paper in the journal Nature.
Concrete has for many years been a contentious material in architecture and is estimated to be responsible for as much as eight per cent of carbon emissions globally.
Other recent low-carbon solutions have included Seratech's concrete made with carbon-sequestering silica and University of Colorado's concrete made with the help of algae.